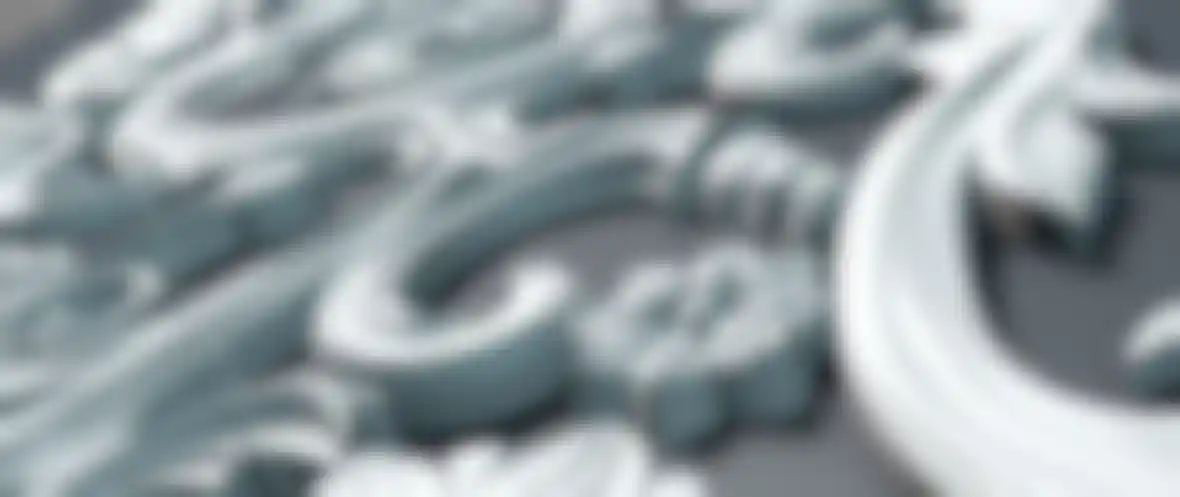
Ornamental Organ Decoration Created with Cinema 4D Wood - the epitome of organic materials - is not the easiest material to bring into shape. But new paths were forged using the right tools and Cinema 4D.
Many historic organs are themselves very imposing and adorned with intricate and very impressive ornamentation. Organs are still being built today, with elaborate decorations. Modern techniques are now being used to create these elaborate designs, which would otherwise be prohibitively expensive to produce.
When the firm of Orgel Mayer was given the job of building a new organ for the philharmonic in Penza, Russia, they wanted to use new methods for creating various elements of the organ's decoration. The organ was designed and built using traditional methods but the decorations were first modeled in 3D and milled out of wood using advanced milling machines. German-based 3D Holzdesign, who has numerous years experience in this field, was commissioned to create the decorative wood elements. 3D Holzdesign specializes in creating wooden elements that are otherwise not feasible to produce. 3D Holzdesign's Andreas Weinzierl worked several years to develop a method of milling based on virtual 3D models. Andreas is able to use virtual templates to mill wooden objects, which is exactly what Orgel Mayer needed for its project.
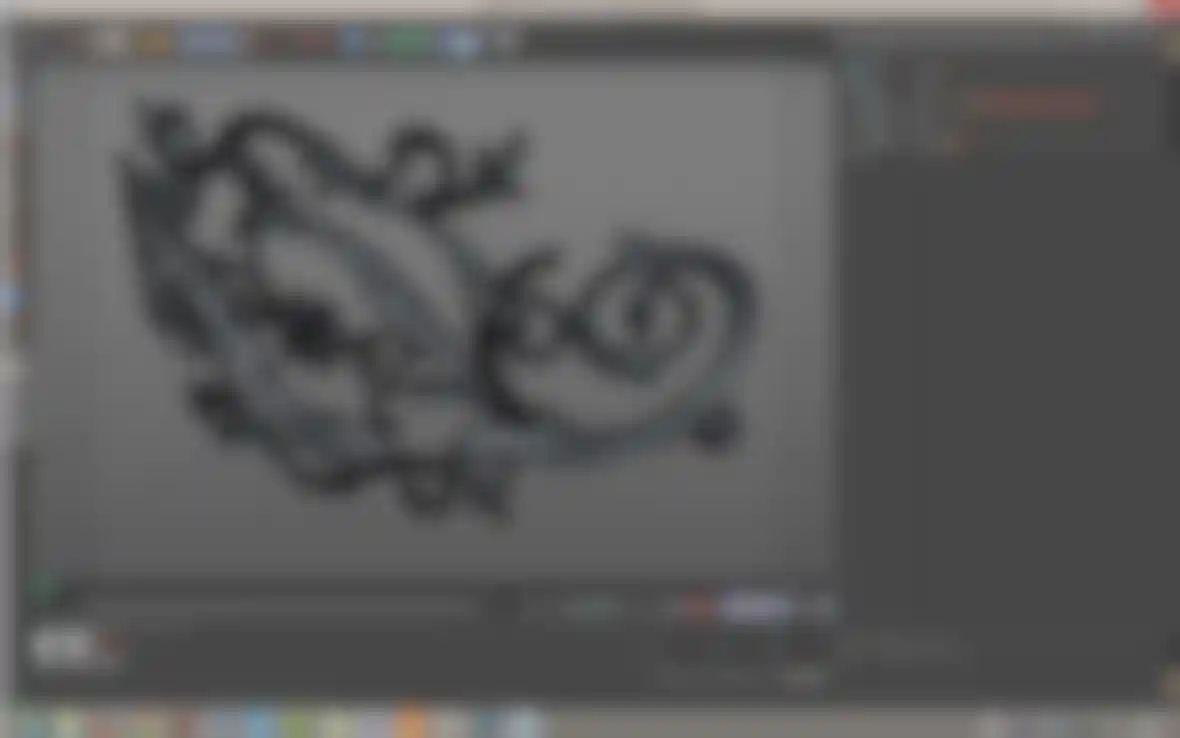
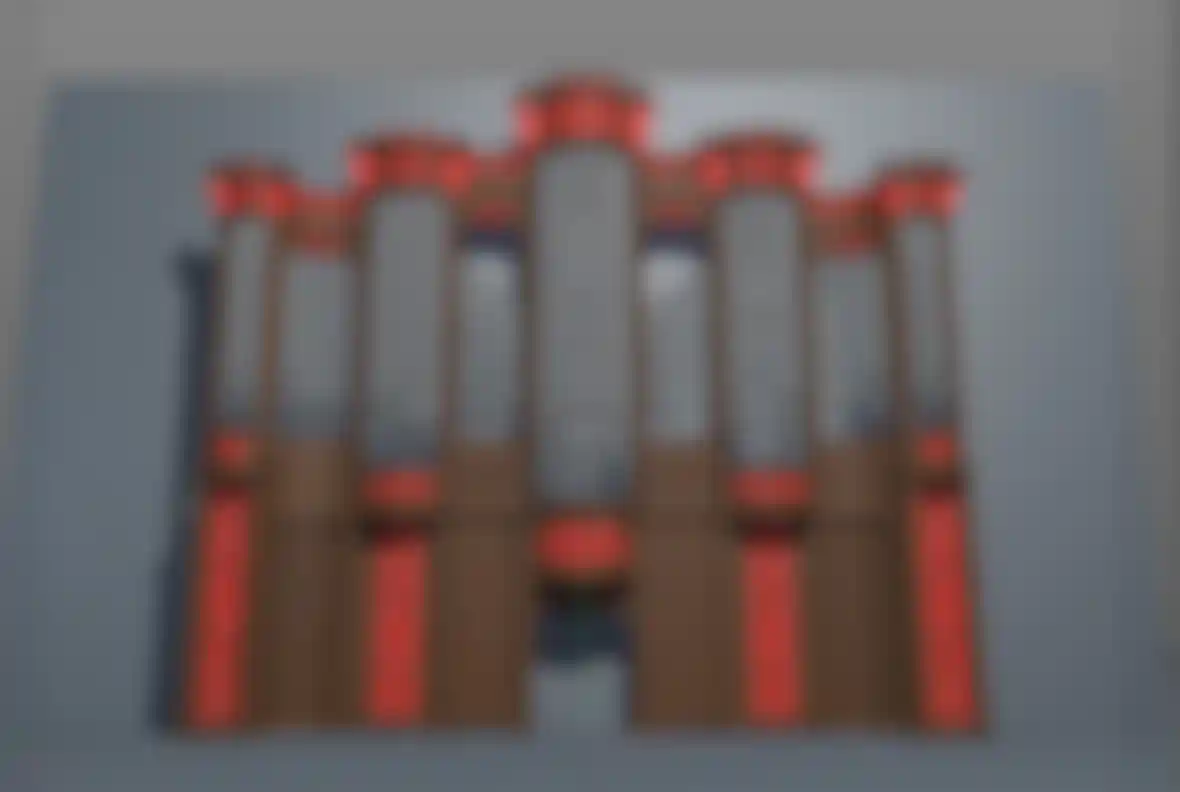
So much for the technical side, all that was needed next were the virtual designs. In the past, this would be done by a wood sculptor who would work from sketches that he would painstakingly carve out of wood. The ornamental design was created by the team at Wiesbaden, Germany-based Augenpulver studios that specializes in 3D design. Paul Kramer and his team created the designs based on a scale CAD model of the organ. "The CAD model of the organ was easily imported into Cinema 4D," Paul recalls, "after which we created basic models for the areas in question, which were then sculpted using Cinema 4D's sculpting tools."
3D Holzdesign took the models created by Augenpulver to mill the shapes out of special blocks of wood using their proprietary connection with the CNC milling machine. The wood was 'special' because it was old and had been stored and dried over a long period of time to ensure that its shape would remain constant, i.e., no shrinkage or distortion. The largest of these blocks of wood was valued at more than €15,000. The finished designs could only be fitted on the finished organ, which was already standing in Penza, Russia - which meant that there was absolutely no room for error! This was made even more of a challenge considering the fact that the milling machine's limitations and characteristics had to be taken into consideration. The diameter of the milling machine's bit predetermined the size of the smallest possible notch or recess. Each tendril had to have its own guide spline within the model along which the milling machine could orient itself. The radian measure also had to be considered, which defines the milling machine's movability and angular position.
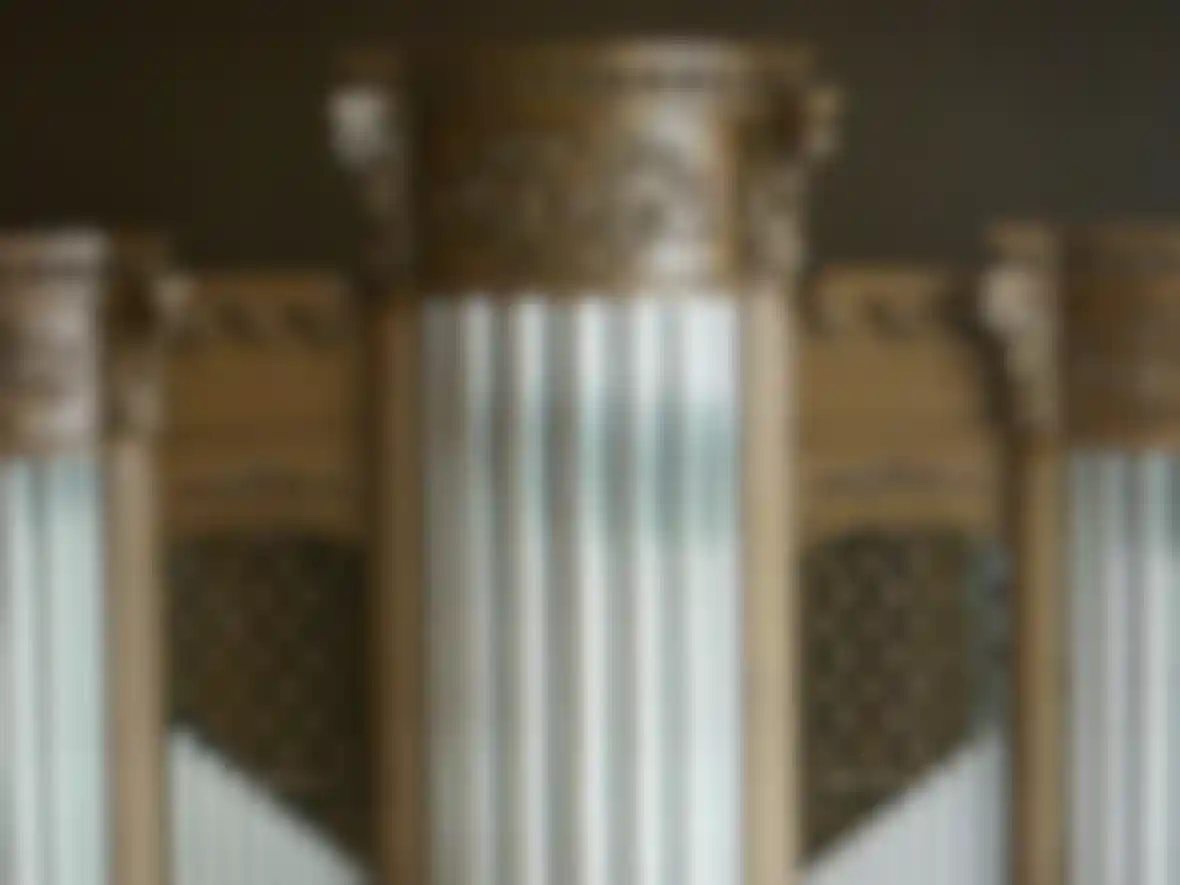
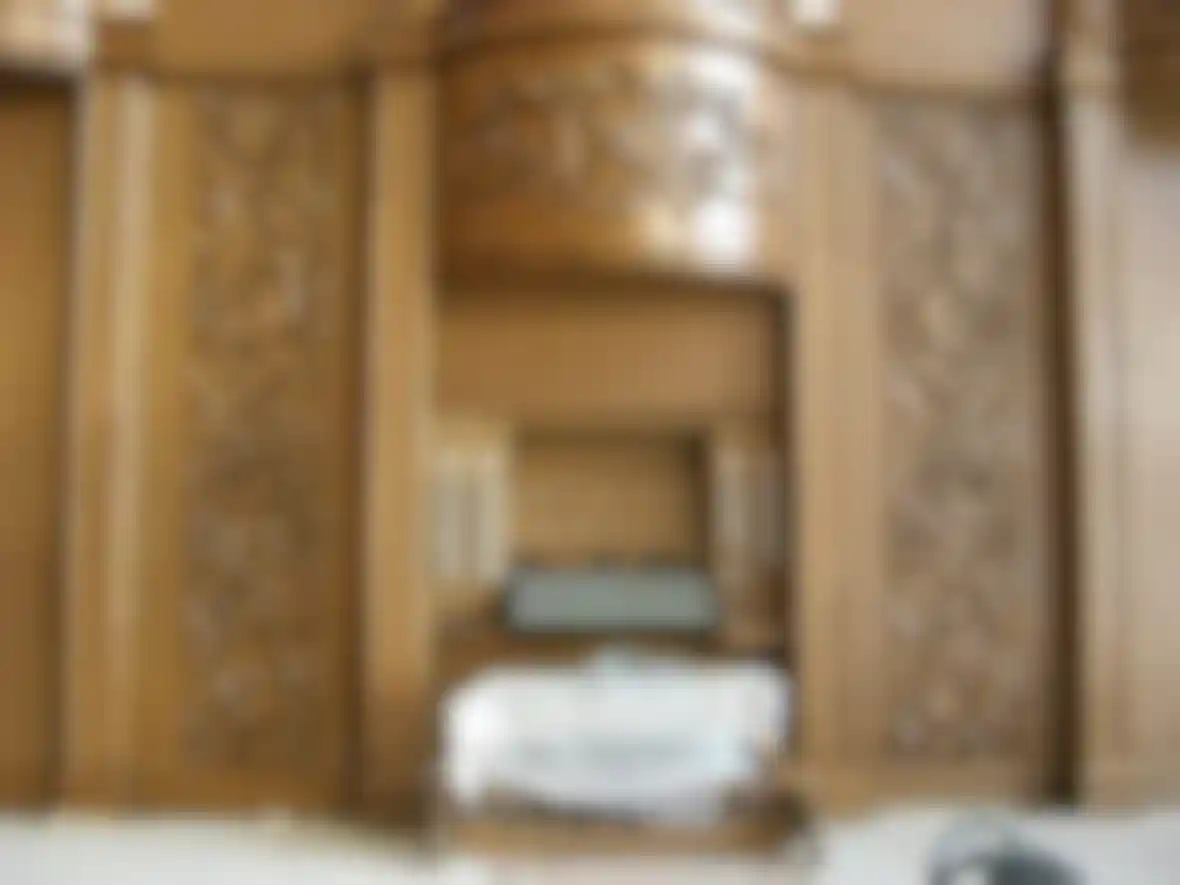
"In the end we were all fascinated by the milled parts! Having virtual models on the monitor is different from holding the finished pieces in your hands. A fascinating experience that was overshadowed by the fact that we didn't know if everything would fit as planned. But we were very elated when the call from Russia came and we were told that everything fit perfectly!", remembers Paul Kramer. "But then, Cinema 4D was the perfect tool for the job: Real units of measure, really good import tools, sculpting tools, and the Object Manager gave us an excellent overview of Generators and Deformers, which made it possible to quickly achieve the results we wanted," concludes Paul and adds: "The team at Augenpulver looks forward to more projects of this type."
Website Augenpulver:
www.augenpulver.eu
Website 3D-Holzdesign:
www.3d-holzdesign.de
Website Orgelbau Mayer:
www.orgelbau-mayer.de